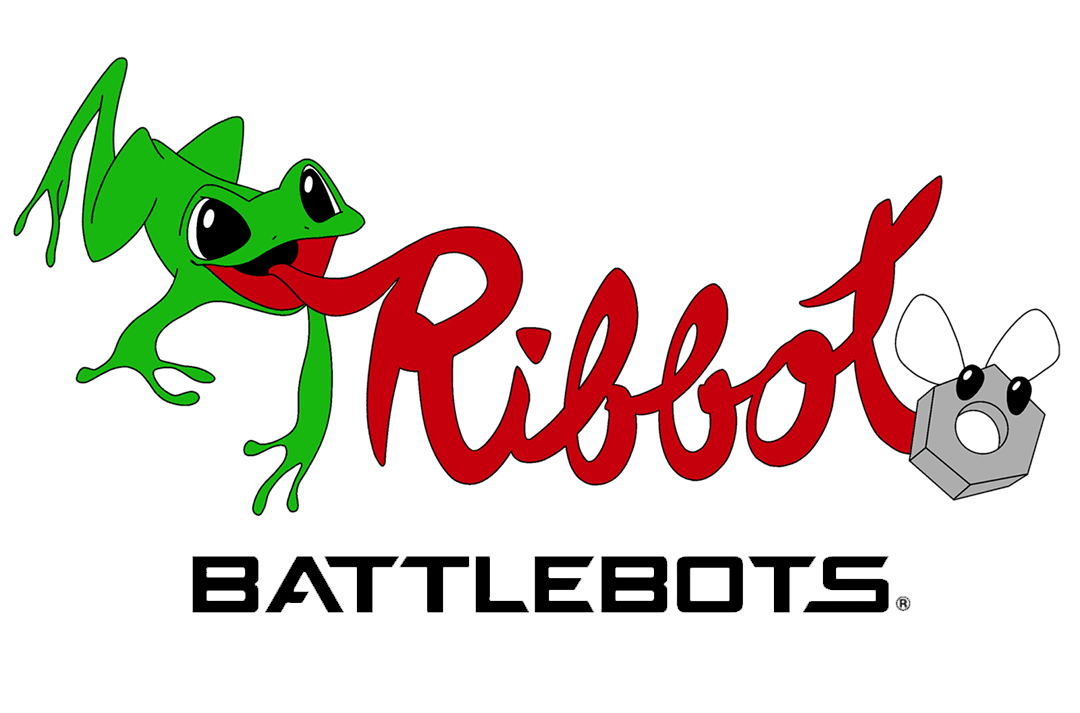
Altium Customer Success
Pushing the Limits of the BattleBots Arena With Ribbot
“Using Altium through this BattleBots experience has given me some great perspective and allowed me to compare some of the tools that we use in the workplace to what Altium can provide. I'd say that Altium is definitely a streamlined approach to board design and allows really great collaboration between the MCAD and ECAD designers.”
Find out how the Ribbot design team used Altium Designer and Altium 365 to push the limits of the BattleBots arena, learn from fiery mistakes, and optimize their combat bot for better results with every competition.
Getting to the BattleBots Arena
BattleBots is the world’s first daily robot-combat show that takes pride in being an intense, fast-moving, family-friendly fight-fest. Participants are selected through an application process to design, build, and compete with their very own fighting robot in pursuit of the coveted Giant Nut and a cash prize.
But, the journey to the BattleBots arena takes mettle—teams need to be resourceful and tenacious with ingenious problem-solving skills. That’s what the Ribbot team learned when they embarked on their journey to the BattleBots arena.
From FIRST® to Flames
Getting their start through FIRST®, the Ribbot team was in high school and applying to colleges by the time BattleBots returned to TV in 2015. While attending Worcester Polytechnic Institute (WPI), the Ribbot team started a small club to compete in the smaller classes, with combat bots weighing in around 1-3 pounds.
By junior year, they were attempting to jump into bigger bots. Their first attempt at a robot greater than 30-lbs was a 120-pound failure. The robot almost immediately caught fire when they turned it on, and they were forced to drop out.
That was the last time the Ribbot team would use an out-of-the-box solution for motor controllers.
Moving to a professional set of tools
“I actually learned on a program called Eagle…My move to Altium was for professional reasons. In my most recent job at an autonomous vehicle company, the primary tool to design circuit boards is Altium Designer. So, I switched which programs I used in my personal life so that I could gain experience more than just in a professional setting. Now, I use Altium for personal projects as well. There's no better way to learn than on your own time.”
Putting the Right Pieces Together With Altium
After realizing their failure was largely due to an off-the-shelf part, the Ribbot team decided their next bot would be built with custom parts they could rely on. This was when they decided to apply for a chance at BattleBots. This was also when they implemented Altium 365 and Altium Designer—two tools that would prove invaluable in helping them make a run at winning the Giant Nut.
A 250-lb robot was a total shot in the dark considering up until then the team hadn't attempted anything above 120 lbs… and that caught fire. With so many lessons learned in real-time, knowledge-transfer and communication between MCAD and ECAD engineers was imperative to making their next bot the best it could be. MCAD CoDesigner—as part of Altium 365—played an especially large role in easing the design process by making it possible for team members to seamlessly communicate, collaborate, and iterate during their late-night working sessions.
According to Team Lead and Mechanical Engineer, David Jin, “one of the biggest advantages that I've found while using MCAD CoDesigner is that when passing a board back and forth between ECAD and MCAD, the references on MCAD, especially SOLIDWORKS in particular, aren't broken. And that's just such a huge increase in efficiency, where before when we were exporting STEP files and sending those back and forth, SOLIDWORKS really isn't capable of importing a new STEP file and then recognizing what references should be carried over.”
Jin adds, “as a result, if you design with any sort of reference to geometry, everything is broken. Every time you import a new STEP file, you have to manually, individually go through, and relink each of the references. While using MCAD CoDesigner, this is no longer a problem. If the EE moves a hole, it doesn't break the reference in SOLIDWORKS when it imports, it's still there. Any reference geometry of that hole will still reference that hole. That's just like such a convenient feature. It allows us to go back and forth so much quicker without constantly fighting SOLIDWORKS, and trying to fix models. In addition, we've had some weird issues in the past, where features would export strangely when trying to move between ECAD and MCAD. That was also a pain because things that were supposed to be circular were not circular, and other issues like that. And we have not had any issues like that while using MCAD CoDesigner."
On the first iteration of their new, fully-customized motor controller solution with off-the-shelf motors, only one motor controller burned out and the team was invited back to compete in 2020… with some adjustments.
“They banned most of our frog, our frog shell caused some filming issues in 2019” said Jin. That’s because the frog shell was made out of 23 lbs of foam and every time it got hit, foam was ejected across the arena. Foam was banned from being used on the outside of robots after Ribbot’s debut.
Coming Off the Ropes
In 2020, Ribbot returned with a lighter-weight hard plastic solution for the frog and upgraded motor controllers. The most significant development, however, was adding a communications module to monitor the motor controllers on the robot live during the match—something they were able to implement with the help of Altium Designer.
According to Jin, “that was nice for us to diagnose failures because we had a log of what was happening inside the robot for every match. Even if it doesn't help you win a match in the moment, it helps you learn what went wrong so you can fix it for future matches.”
Ribbot was first to bring online telemetry and recording to the arena as most were still doing this offline.
“The issue with that is what happens when your robot ends in fire and is just in a pile of parts? The information is gone, you lost it. So, we took an approach to stream live and record outside the box on a tablet. We won’t lose the data if the match goes catastrophically,” added Sorensen.
This technology gave the Ribbot designers confidence in the robot’s health during the match. They knew if the frog could push harder or needed to pull back to keep motor controllers from burning. Having access to this real-time information gave Ribbot the competitive advantage they needed, making 2020 their smoothest season yet. It was the best they had ever done even though the base robot was similar to what it had always been with small internal tweaks.
Faster design collaboration with Altium 365
“Altium 365 allows for easy collaboration and sharing of our designs, so I can share with the entire team, the schematics, even the board, without my other teammates having or needing to have Altium Designer installed on their computer. This allows for incredibly fast design reviews and feedback from all of our designs.”
Eyes on the Prize
In October 2022, Ribbot was deemed ready to compete in BattleBots World Championship VII—ranking #11 in the Pre-Season Power Rankings. Among its upgrades, Ribbot now sported red hubs and more detailed eyes with red irises. The team also partnered with the animal conservation organization; SAVE THE FROGS!, with their logo adorned on Ribbot's vacuum-formed shells. Ribbot lost three consecutive battles, but managed to keep their hopes alive with a knockout victory.
By learning from their fiery mistakes and using the data they collected from past bots to iterate on their designs, the Ribbot team is entering the BattleBots semifinals with confidence they may finally have their champion.