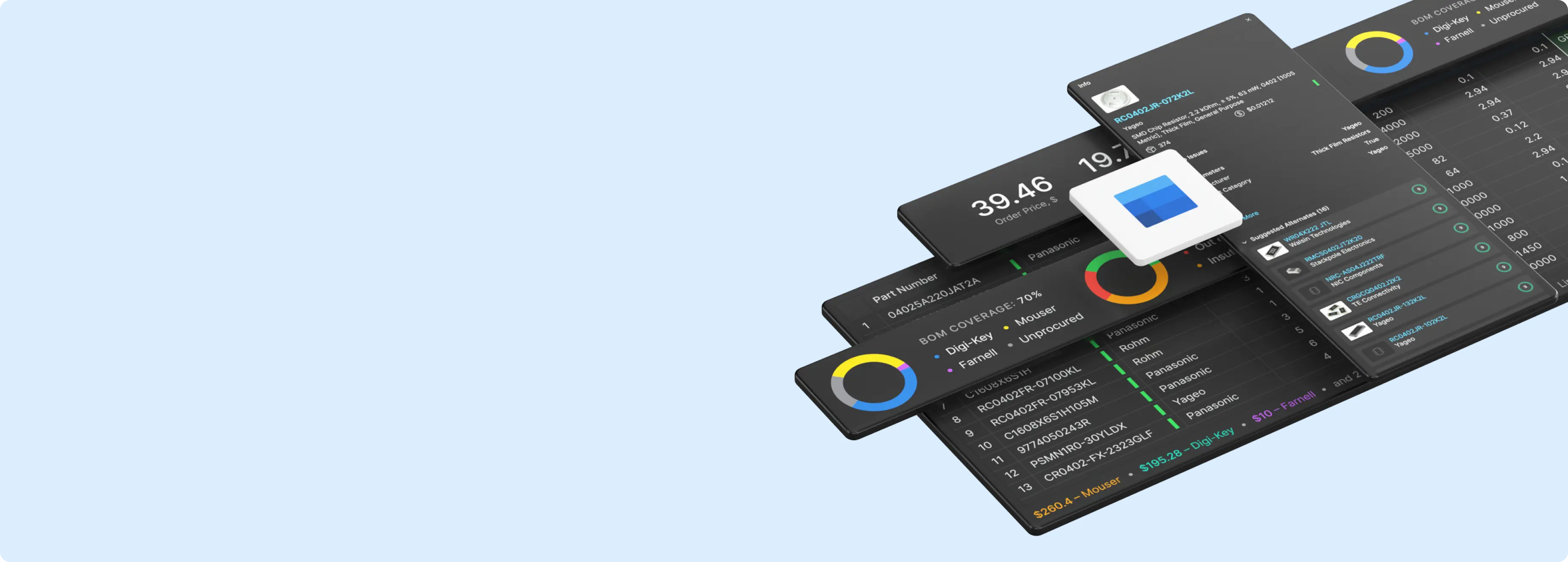
Unlock
the Secrets
of BOM Management
Elevate your supply chain and procurement
skills from novice to pro
skills from novice to pro
Summary
Every electronic product requires an important document before manufacturing: a bill of materials (BOM). The BOM includes information about the parts that will be used in the fabrication and assembly of a new product.
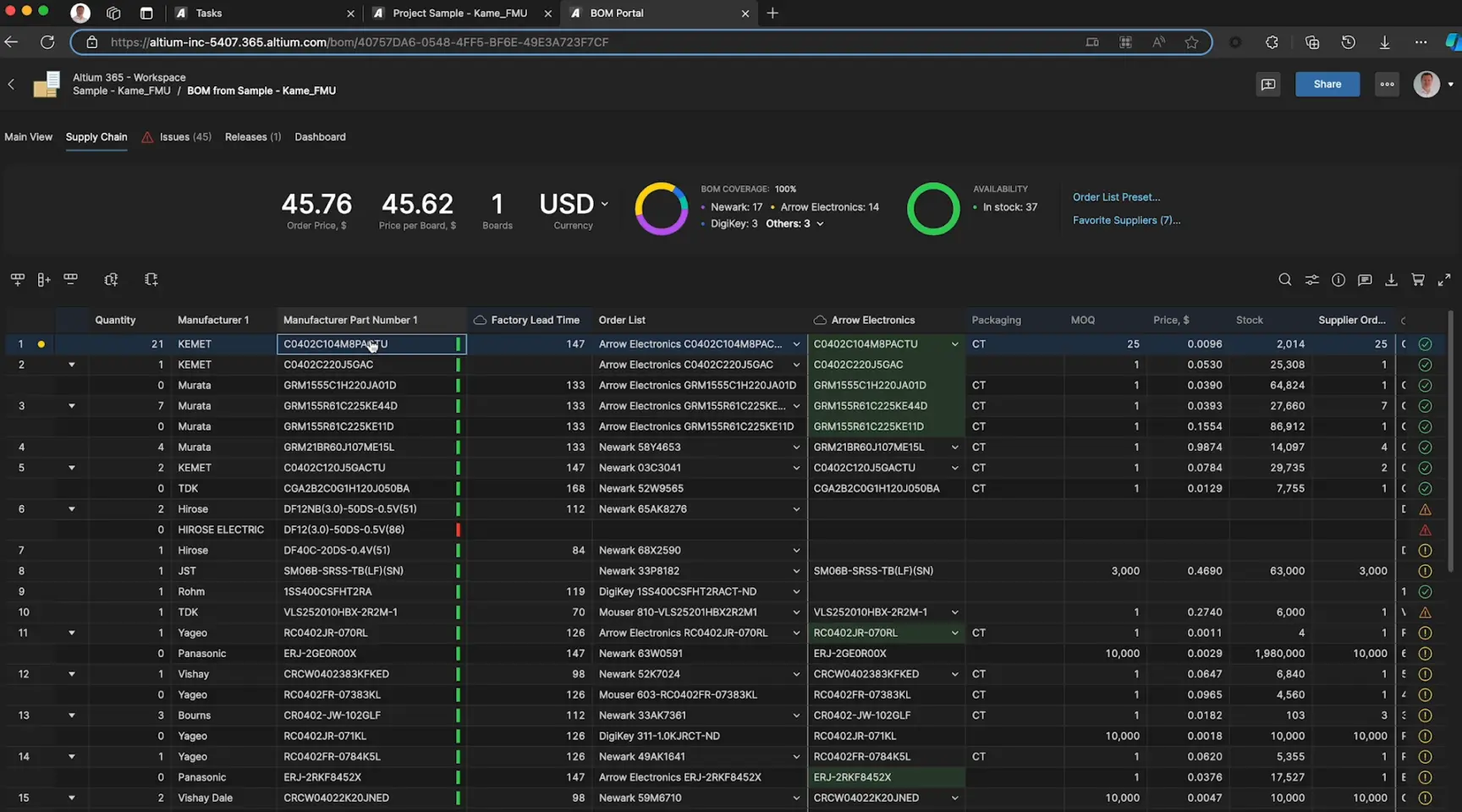
While a BOM initially originates from your EDA software, it evolves into a critical living document that connects design, procurement, and manufacturing throughout the product lifecycle. It's the central reference point that guides part selection, procurement decisions, and supply chain management from initial design through production. There are many types and formats of BOMs used in different industries, but they all play the same important role in guiding procurement and assembly.
This BOM management guide dives deeply into everything hardware engineers need to master the creation and management of BOMs, starting from the fundamentals to BOM management software advanced strategies for managing complex, dynamic supply chains. The BOM for a new product is the starting place for controlling cost, streamlining procurement, and maintaining the designer’s intent for manufacturing; as such, it needs to be monitored and managed throughout a product’s lifecycle. This guide will give design engineers an overview of how successful design teams manage their BOMs, as well as how these processes impact procurement and product lifecycle management.
What Is a Bill of Materials?
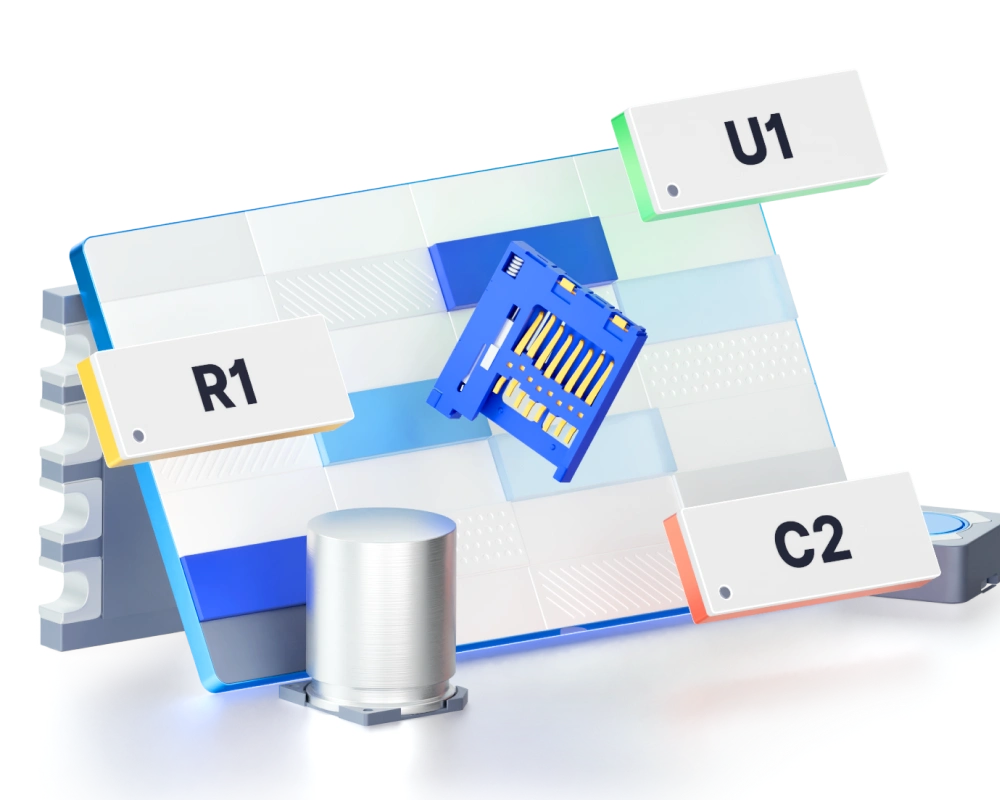
A product’s BOM is a structured list of all parts, materials, and assemblies required to manufacture a product and bring it to market. For PCB designers, a BOM contains all the electronic part numbers that will be used in the PCB Assembly (PCBA).
Every BOM for an electronic device includes, at a basic level, the following information:
- Internal part numbers and quantities
- Reference designators for each part
- Manufacturer names, part numbers, and acceptable alternates
- Supplier names, supplier part numbers, and pricing information
- For some assemblies, a BOM contains a PCB part number and materials
The BOM is more than a shopping list; it acts as a single source of truth connecting design, procurement, and manufacturing. It’s important to have all of the part information in one place, so BOM managers can make sense of potentially confusing information like multiple part numbers for the same component.
Today’s BOM can be much more than an Excel sheet with static part numbers; it has evolved into a living document that provides dynamic information directly from the electronics supply chain. Design teams can use real-time data visibility when planning purchases, managing production orders, and monitoring lifecycles of critical electronic components. Modern cloud BOM management software enables a level of BOM automation that was not possible only a few years ago, and it is driving new levels of productivity within design and procurement teams.
What Is BOM Management?
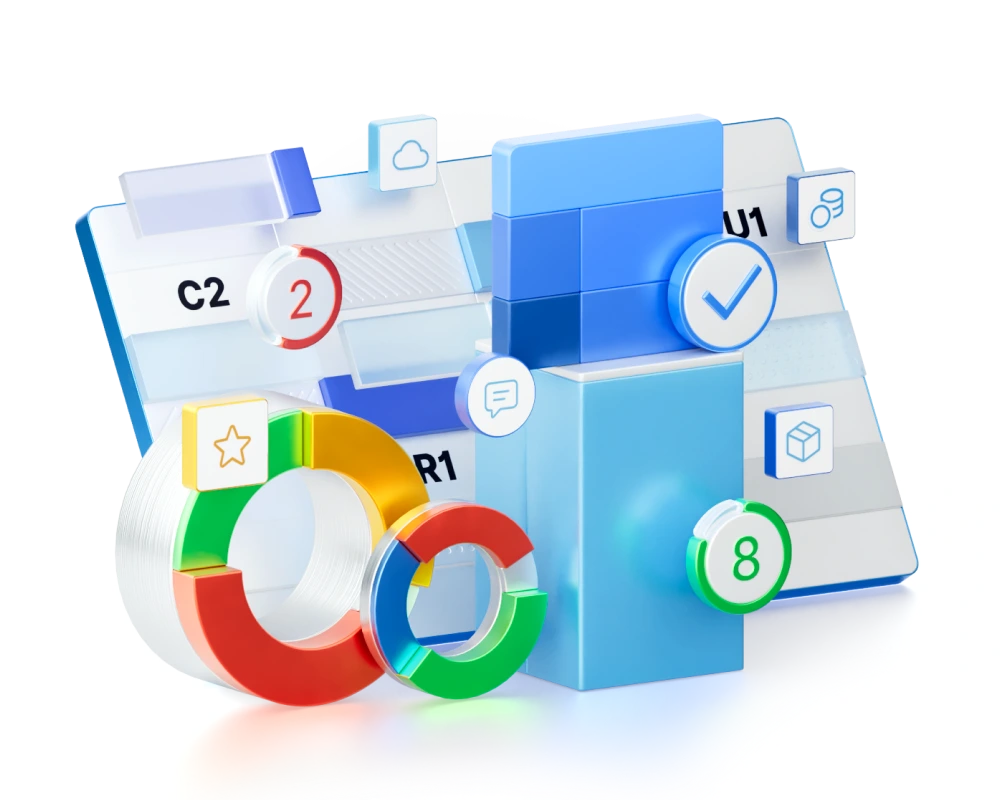
BOM management is the systematic process of controlling, tracking, and maintaining Bills of Materials throughout a product’s lifecycle. While a BOM itself is a comprehensive list of parts, components, and assemblies, BOM management encompasses the activities and systems that keep that information accurate, up-to-date, and accessible across engineering and procurement teams.
At its core, BOM management is the foundation for electronic product data control. It maintains critical component information, including manufacturer part numbers (MPNs), supplier part numbers (SPNs), parametric data, and compliance status. Through revision control and engineering change management, it ensures everyone works from verified component data.
A critical component of BOM management is BOM analysis—the systematic evaluation of component data to identify risks and opportunities. This includes monitoring lifecycle statuses (active, NRND, obsolete), analyzing costs and lead times across suppliers, verifying compliance with standards like RoHS and REACH, and identifying opportunities for component consolidation. Modern BOM management software integrates with supplier databases to provide real-time data on availability, pricing, and alternative parts and can automatically perform BOM analysis to flag issues like end-of-life notifications, compliance problems, and supply chain constraints before they impact production.
The strategic role of BOM management extends across the entire product development process. It bridges the gap between engineering decisions and procurement activities, enabling teams to work concurrently while maintaining data integrity through revision control and change management processes.
Why BOM
Management
Is Crucial
Management
Is Crucial
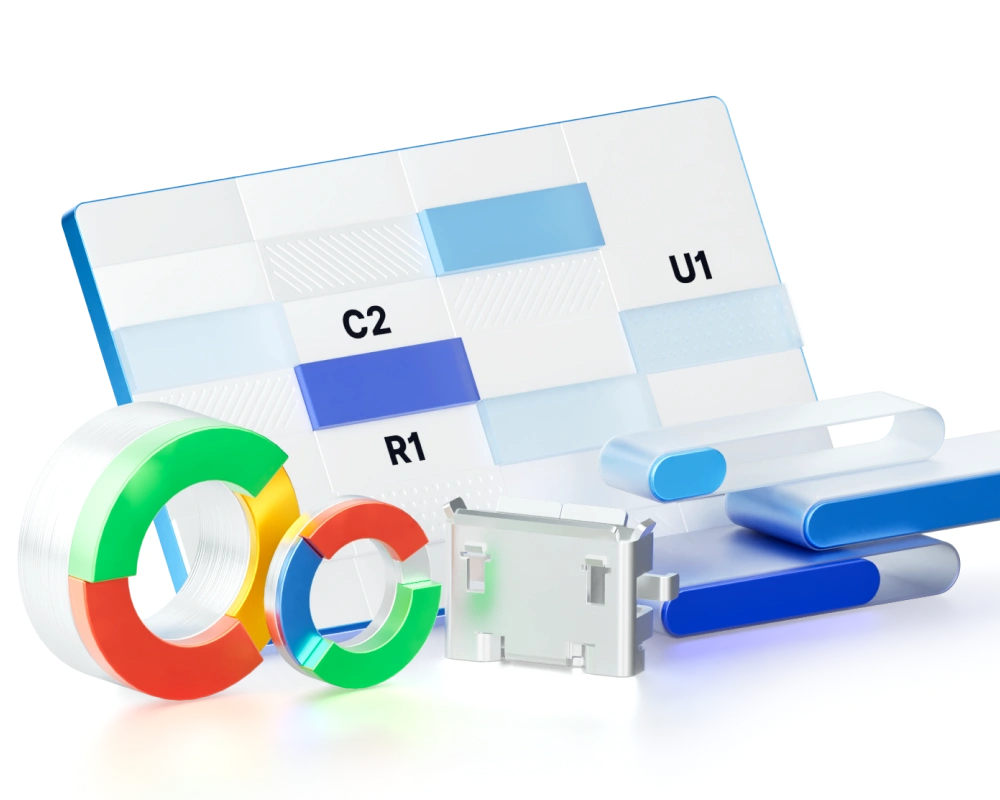
Cost Impact
According to a study by Forrester, engineers can spend up to 159 hours per year performing administrative tasks*, which mostly includes tasks related to procurement and BOM management. These tasks are not something engineers tend to find enjoyable, yet they cannot be delegated. Engineering input is required to ensure that the product is built to specification.
Furthermore, the Forrester study found that 80% of designs require part replacements, resulting in an additional average* of 40 hours of time spent sourcing these parts. This equates to 2.8 PCB re-spins at an average of $46,000 per re-spin**. These manual tasks continue to slow companies' time to market and tax their revenue streams.
Designers should be able to use BOM management software to take advantage of the wealth of digital data inside a BOM, which could help streamline crucial tasks. In a digitally connected world, designers can use the cloud to access real-time technical data on parts, component data on availability, and lifecycle data on part end-of-life schedules that inform supply chain risk assessments. Procurement managers need to track BOM changes and collaborative decisions across departments as part of BOM management. This gives procurement teams immediate visibility into product revisions and their impact on part inventory or purchase plans.
* A commissioned study conducted by Forrester Consulting on behalf of Altium 365. Results are based on a composite organization.
** Lifecycle Insights, 2018
Risk Management
All electronic products involve supply chain risk, but a BOM management platform and process can mitigate that risk. A product’s health can be compromised in a variety of ways:
- Parts can go out of stock or become obsolete
- Supply chain disruptions can impact purchasing and production
- Compliance requirements (RoHS, REACH, etc.) can change
- Quality control problems may require alternate parts
Companies manage these risks better when they leverage BOM software to see all the required supply chain and procurement data directly inside the BOM and they can link that data to schematics and designs.
Market Pressures
Market pressures also demand creative and precise BOM management processes. In particular, accelerated development cycles and design-to-cost pressures drive the need for real-time supply chain data visibility, specifically data related to prices and inventories held by global distributors. Electronic products have become far more complex, with some products having 100x as many parts as earlier generations of the same product. In an environment where globalized production creates global supply chain challenges, design teams need BOM management tools that help them optimize costs across their supply chain and product portfolio as they plan to scale up production.
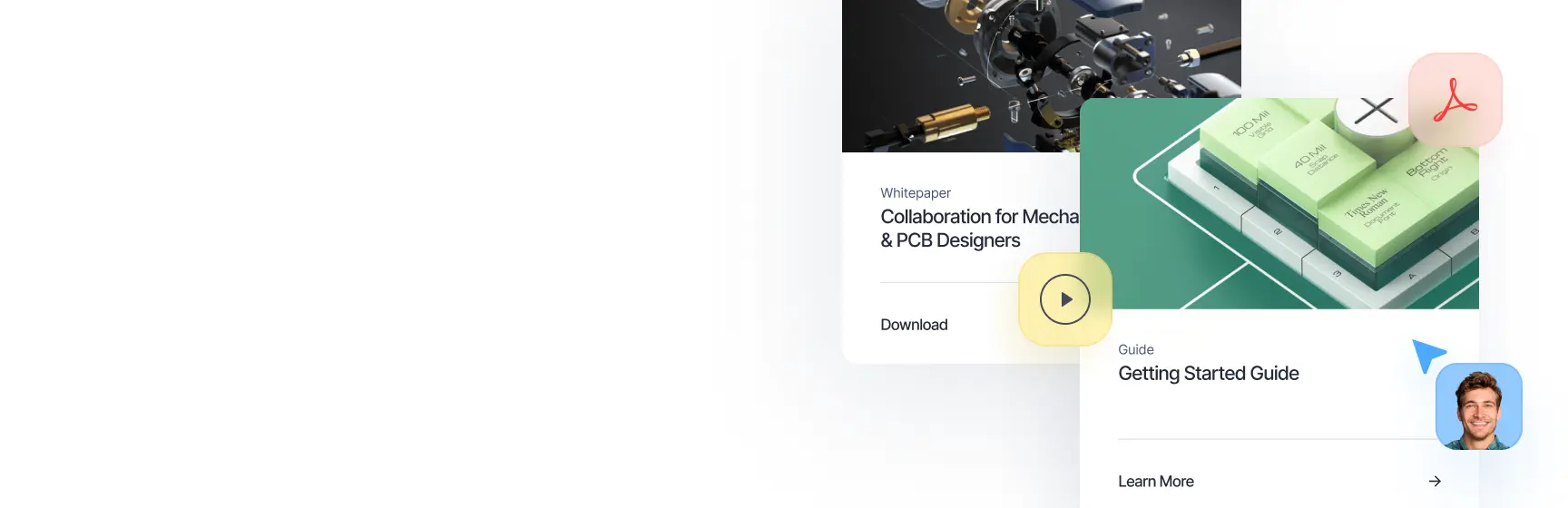
Main BOM Management Challenges
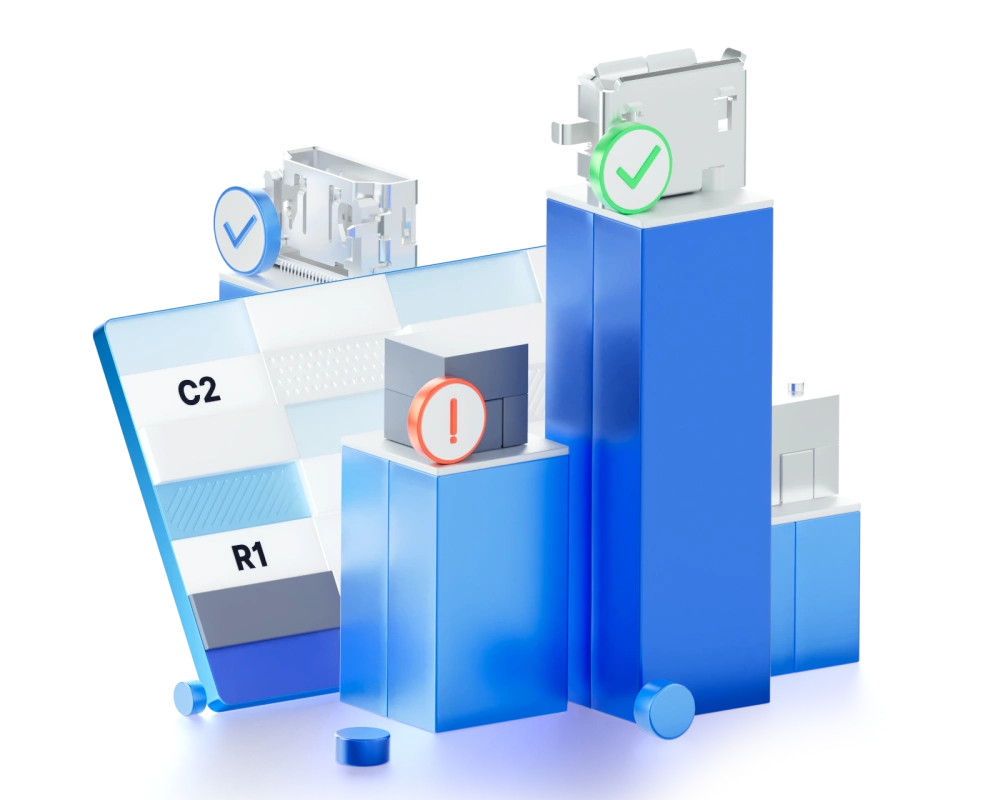
Designers, procurement leaders, and engineering managers spend too much valuable time updating BOM data across multiple products. In the past, this was done by manually updating supplier and lifecycle information in libraries and re-exporting BOMs as spreadsheets. Because everything was done manually, multiple reviews were required to catch human errors and assure the accuracy of BOM data. When BOM reviews scale across multiple products, it creates more manual administrative work.
Although EDA software and product data management (PDM) platforms have changed to handle the growing complexity of managing electronic parts supply chains, BOM management technologies have not. Design teams still need to:
- Maintain BOM accuracy across multiple revisions
- Synchronize BOM data between departments and tools
- Manage part alternatives and substitutes
- Enforce version control and track changes of product data
Supply Chain Blindness Creates Inaccurate BOMs
Even great teams that attempt to manually enter data into their master BOM document are going to make mistakes. Of course, someone can update supplier information in the part library, but this is much more time-consuming and requires updates to the design data before re-exporting a BOM. Manual fixes become cost-prohibitive when a company has to maintain many BOMs across many products and versions. Inaccurate and outdated BOMs cause challenges that impact a design team or procurement department’s velocity as they plan production and execute purchases. Some of these challenges include:
- Incomplete part inventory and pricing data
- Delayed part obsolescence notifications
- Uncertain lead times for parts used in production
- Inconsistent part data from different suppliers
When teams manage BOMs in Excel sheets, design and procurement will never know if the supplier or lifecycle information continues to be accurate. This is why BOM management tools must always be connected digitally to the highest quality part data repositories for technical data and lifecycle statuses.
Data Quality and Integration
Third-party data providers can make current part data available to design and procurement teams so they can overcome their limited access to technical specifications and lifecycle data. Altium 365 integrates streaming data services for digital components into its BOM management tools. This helps BOM managers keep inconsistent or outdated part data out of their BOMs. These integrated third-party data platforms also provide traceable compliance information and lifecycle status information, as well as access to product change notifications (PCNs). A digital link to the supply chain with real-time data provides this information directly inside the company’s BOM software so team members don’t need to toggle between multiple apps or web pages. Altium products also bridge communication gaps between teams. Manual data entry only occurs when a part is created in a library; all future supply chain updates are automatically fed into the BOM and parts libraries rather than being entered manually. By eliminating so many manual tasks, teams can transform their PCB BOM management processes and spend more time focused on designing competitive products.
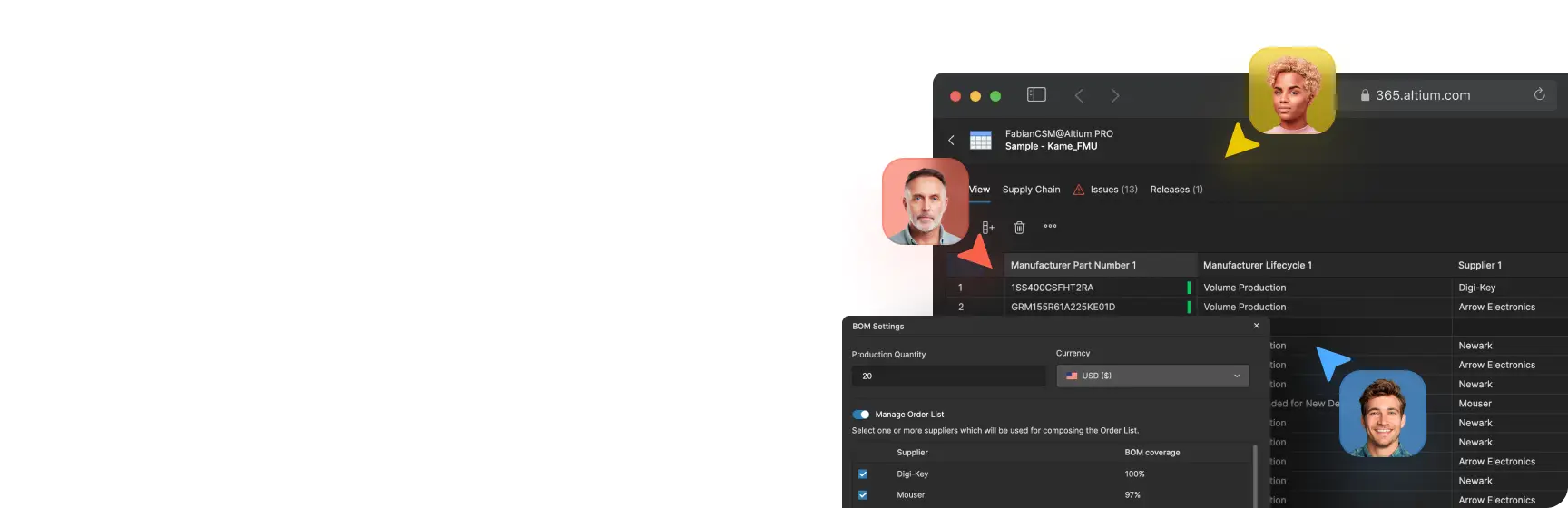
Best Practices for BOM Management
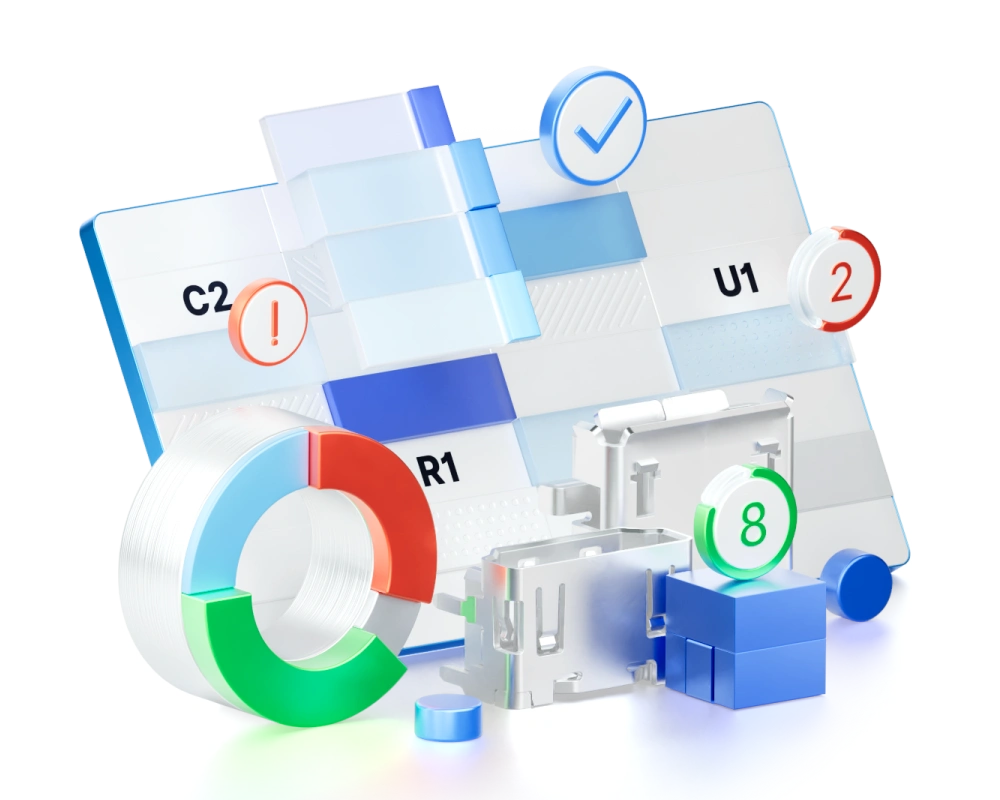
In the world of PCB design, designers use EDA software to implement best practices for PCB BOM management. Managing the data in a BOM starts with ensuring data in a parts library is accurate and that parts have a link to real-time supply chain data from preferred suppliers. Project stakeholders can implement their management processes in a PDM platform while also enforcing version control and ensuring that collaboration happens in a secure environment. Teams need a better way to share information than the emails and PDF attachments that they’ve used for years.
What should design teams do as part of their BOM management process? BOM management should be part of a product lifecycle management process that specifically focuses on part and supplier information as it relates to manufacturing electronics assemblies. Teams will need to periodically review and update BOMs based on lifecycle changes, inventory changes, and design revisions. A BOM management tool that pulls data from the supply chain and links directly to libraries and projects streamlines the maintenance of accurate BOM data.
Within a BOM management process, a team should attempt to reach these goals:
Enforce a Consistent Library Structure
- Maintain a consistent part numbering system for library parts
- Define required parameter fields for library parts
- Enforce review and revision control procedures
- Assign one team member to oversee part release approval
Process Management
- Involve procurement teams early in the design process
- Perform regular BOM reviews for each project
- Implement change management procedures
- Roll out a new part creation and review process
Software Integrations
- Guarantee ERP/PLM connectivity
- Provide part database links
- Implement change management procedures
- Display supply chain data in library parts
Data Integration Best Practices
- Link real-time data from the preferred supplier directly to library parts
- Standardize on a single database and management solution
- Establish regular data validation and cleanup policies
- Follow multi-source data verification strategies
Engineering teams are responsible for developing processes to achieve these goals. Design, procurement, and data management tasks are all linked together through a company’s EDA platform and their ERP/PLM tools.When this is done correctly, design teams see the supply chain data they need inside their PCB design software, BOM management tool, and parts libraries. This makes BOM management faster, more automated, and more accurate.
BOM Management Tools
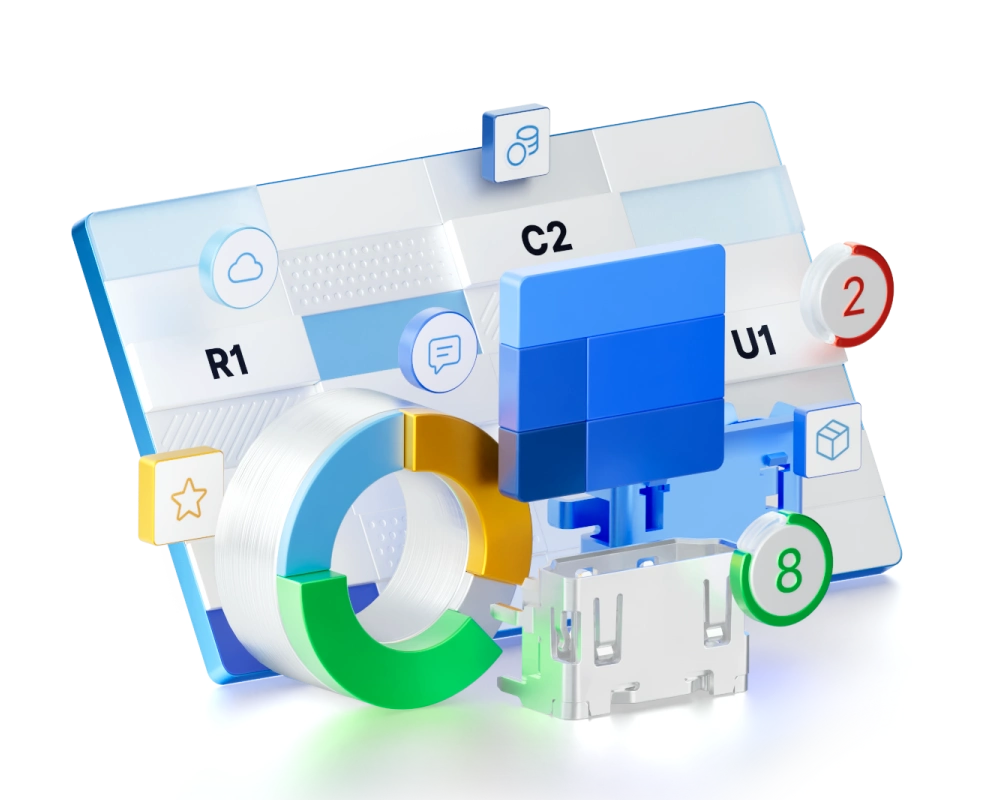
Given all the data and part management tasks required to maintain electronic products, PCB designers and procurement professionals need a BOM management software that complements their company’s design process and streamlines management tasks. Instead of using third-party software or trying to use an ERP system, use a platform that integrates directly with your EDA software. This ensures users have access to the supply chain data they need, integrated within a collaboration solution for electronics design.
BOM Portal in Altium 365 combines PCB BOM management with integrated supply chain data. BOM Portal allows users to upload a BOM or create the BOM directly from the PCB project. The system automatically pulls supply chain data into the BOM. Instead of searching for this information manually, users see current supply chain data within their work environment. They know that the following will be accurate and available for important project decisions:
- Pricing and inventory information
- Lifecycle status for each line item
- REACH/RoHS compliance confirmation
- Suggested alternate part numbers
- Data aggregated from preferred suppliers
- Integration with PLM and ERP systems
- Group-level and user-level access control
- Change tracking and version control for each BOM
All supply chain data is supplied by industry-leading data aggregators like Octopart, IHS Markit, SiliconExpert, and Z2Data, ensuring designers have up-to-date, accurate information in real-time.
Thanks to the collaboration and version control features in Altium 365, stakeholders from across an organization can share, view, and edit a BOM while planning purchases for upcoming PCB manufacturing runs. Once a PCB project and its BOM are finalized, data packages can be released to a contract assembly house or third-party logistics provider using the platform’s built-in sharing features.
We built Altium 365 specifically for electronics design teams and it integrates directly with PCB design projects in Altium Designer. Altium 365 and BOM Portal give you constant access to supply chain data, part management features, and version control, for comprehensive supply chain management for PCB projects. See how BOM Portal on Altium 365 can help teams streamline design and procurement in a secure, easy-to-use cloud platform.
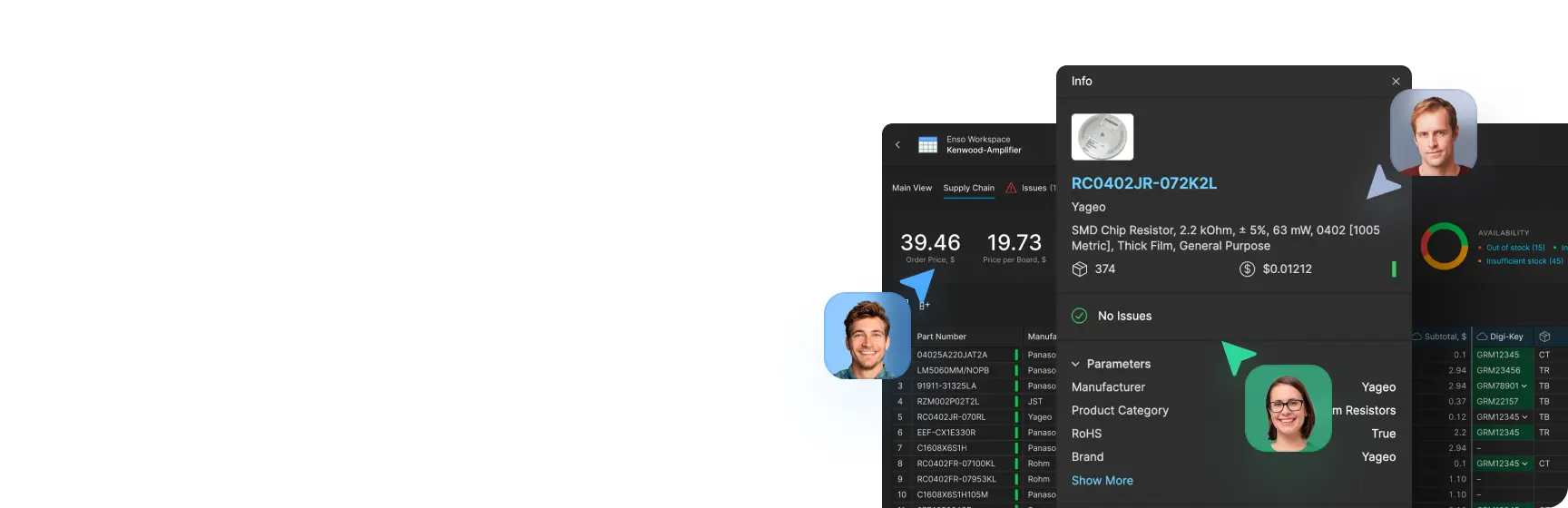
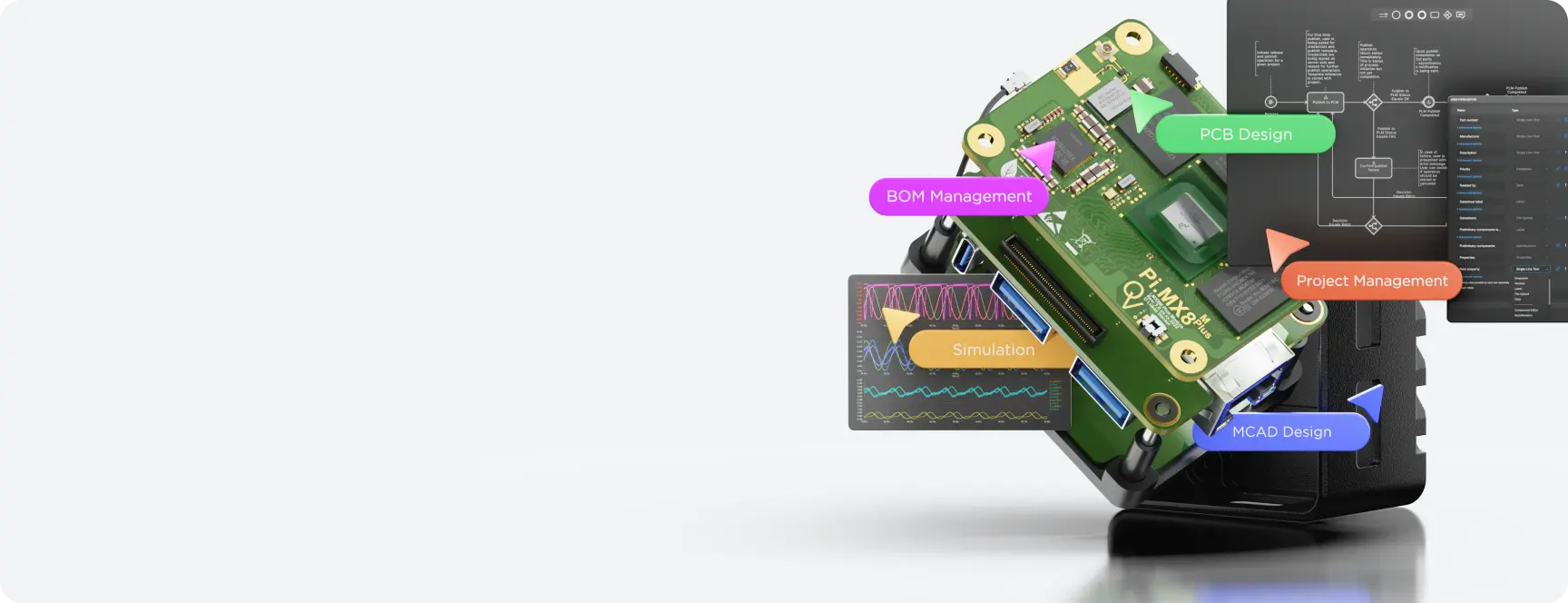
Check Our Education Hub!
Free Webinars, Extensive Courses, and Much More Available to You.
More Recommended Reading
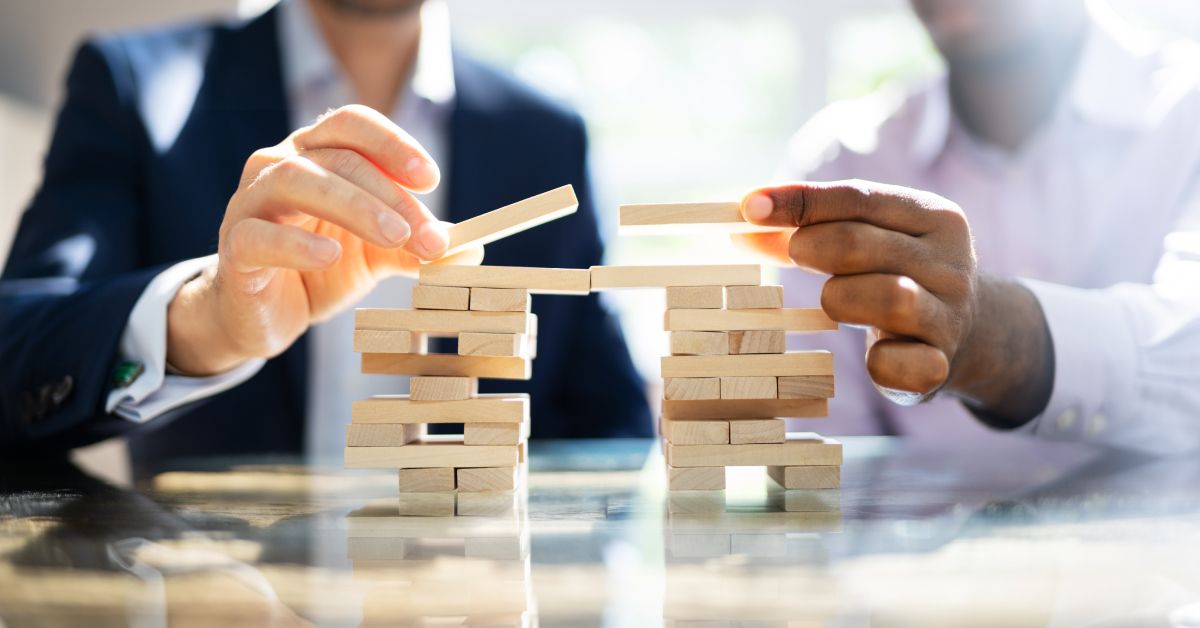
Article
How to "Shift Left"?
Connect procurement and engineering to run the timelines and accelerate time to market smoothly.
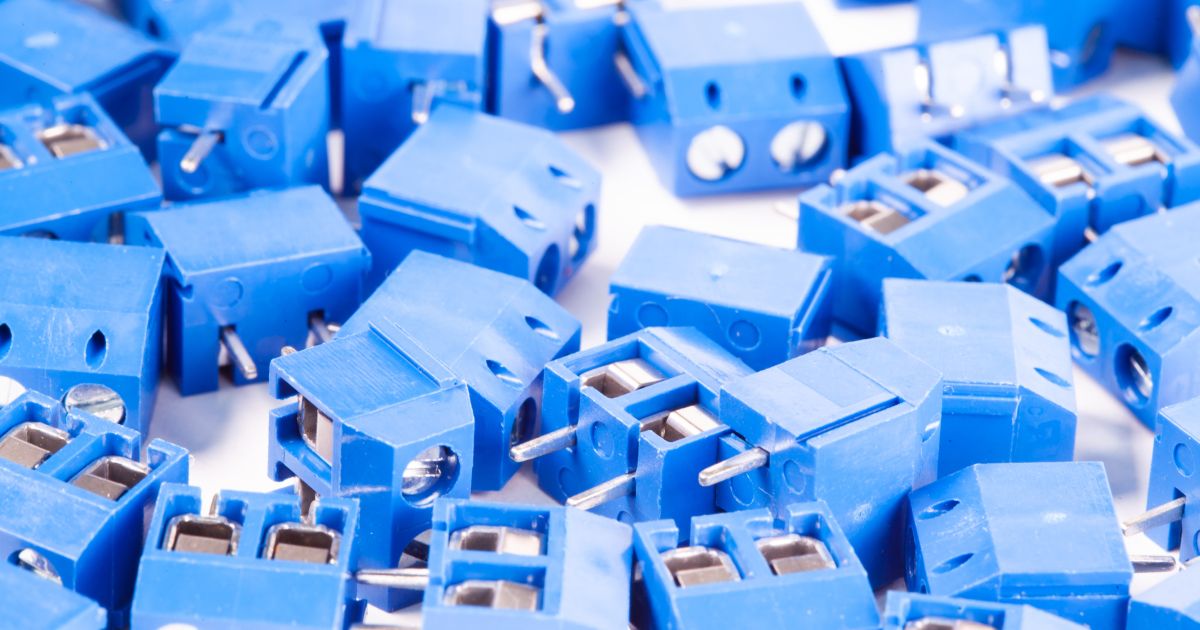
Article
A Game Changer for Design Engineers and Supply Chain Optimization
Optimize BOM management with Altium 365 BOM Portal. Reduce errors and streamline compliance.
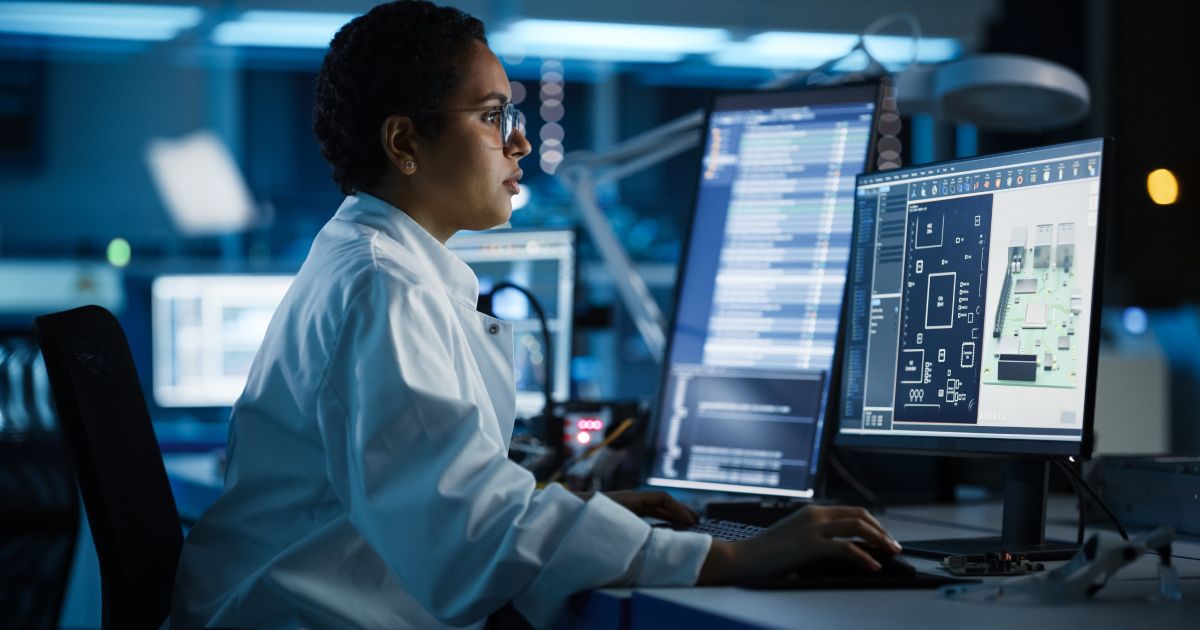
Article
PCB Design Excellence Through BOM Management
Discover tools to boost efficiency, cut costs, and streamline workflows in BOM management.
Frequently Asked Questions
BOM Portal provides version control and allows users to create “releases”. Each change is documented with user information, a timestamp, and a comment. You can compare revisions side-by-side and track the complete history of changes.
BOM Portal proactively monitors component lifecycles by:
- Providing real-time component lifecycle status
- Automatically flagging at-risk components
- Offering insights into years-to-end-of-life (YTEOL)
- Suggesting qualified alternate parts
- Enabling impact analysis across all your BOMs
- Integrating with component databases for up-to-date part information
BOM Portal bridges the gap between teams through:
- Shared access to real-time BOM data
- Built-in commenting and notification systems
- Clear workflow processes for reviews and approvals
- Visual indicators for BOM health and issues
- Ability to create and track change requests
- Direct access to design files and documentation
- Integrated supply chain insights for informed decisions
BOM Portal enriches BOMs with:
- Component lifecycle status
- Compliance information (RoHS, REACH, and more)
- Real-time pricing and availability
- Manufacturer information
- Risk assessments
- Alternative parts suggestions
- Supply chain insights
- Parametric data
BOM Portal streamlines alternatives management by:
- Automatically suggesting compatible alternatives
- Showing real-time availability across alternatives
- Maintaining a database of approved alternatives
- Enabling quick impact analysis of substitutions
- Offering risk assessment for each option
Yes, BOM Portal offers customization through:
- Configurable workflows and approval processes (extra app)
- Custom fields and data requirements
- Custom BOM templates
- User role and permission settings
- Integration with existing enterprise systems
BOM Portal maintains data quality through:
- Automatic data validation and enrichment
- Integration with trusted component databases
- Standardized data entry formats
- Built-in error checking
- Regular data updates
- Duplicate part detection
- Consistency checks across BOMs
BOM Portal offers comprehensive analytics including:
- BOM health scores
- Component risk assessments
- Supply chain visibility metrics
- Cost analysis and tracking
- Compliance status
- Usage analysis across BOMs
- Change frequency metrics
- Time-to-resolution tracking
Create a Managed BOM by either:
- Importing your existing BOM files (drag & drop CSV/Excel files)
- Creating from existing Altium 365 projects
BOM Portal automatically:
- Maps your columns (part number, manufacturer, quantity, etc.)
- Enriches your BOM with component data
- Identifies potential issues and risks
Review and manage your BOM:
- Check the BOM health dashboard
- Review any warnings or errors
- Find alternative parts if needed - or add alternates automatically
- Share with your team for collaboration
Source and order components:
- Compare prices across suppliers
- Check real-time availability
- Use Octocart to add parts directly to supplier shopping carts (Mouser, DigiKey, Newark, etc.)
Optional advanced setup:
- Configure custom templates
- Set up lifecycle states for BOM review process
- Connect with your component library
- Enable additional data integrations
Address obsolescence proactively through:
- Regular monitoring of component lifecycle status
- Setting up automated alerts or dashboards for end-of-life notifications
- Maintaining a database of qualified alternate parts
- Including lifecycle risk assessment in component selection
- Planning for component transitions before they become critical
- Using real-time component data to make informed decisions
Enable effective collaboration by:
- Using a centralized BOM management platform
- Implementing clear workflows and approval processes
- Providing real-time access to the latest BOM data
- Establishing clear roles and responsibilities
- Using commenting and notification features
- Maintaining change history and tracking
- Creating standardized processes for communication between engineering and procurement
A complete BOM should include:
- Part numbers (manufacturer and internal)
- Descriptions and specifications
- Quantities and units of measure
- Reference designators
- Manufacturer information
- Supplier information
- Cost data
- Component status and lifecycle information
- Compliance certifications
- Assembly notes or special instructions
- Revision history
Effective part alternative management includes:
- Maintaining a database of pre-approved alternates
- Documenting specific qualification criteria
- Verifying form, fit, and function compatibility
- Tracking price and availability across alternatives
- Implementing a formal approval process for substitutions
- Regular review of alternate parts status
Track BOM changes through:
- Formal change management processes
- Automated version control systems
- Clear documentation of change reasons
- Impact analysis before implementing changes
- Notification system for affected stakeholders
- Regular BOM review meetings
- Change history logs with full traceability
BOM software should track these key performance indicators:
- BOM accuracy rate
- Component availability percentage
- Number of engineering change orders
- Time spent on BOM management tasks
- Component obsolescence rate
- Supply chain disruption incidents
- Cost savings from early risk identification
- Time from design to manufacturing release